Sustainability is undoubtedly the need of the hour. It holds immense significance in the manufacturing of textile products as it addresses the urgent need to protect the environment and promote responsible practices within the industry. The textile industry is currently included in the top 5 most polluting industries. Embracing sustainability in textile manufacturing involves rapidly expanding recyclability of existing materials as well as developing new sustainable alternatives to existing materials. As a designer involved with textiles, I believe that by adopting such sustainable techniques, the textile industry can contribute to the preservation of natural resources and the reduction of pollution.
Being a design professional myself, I understand that the aesthetics of a product play a crucial role in influencing consumers and enhancing the overall user experience. We all want beautiful products which enable us to express our own individuality. Would you buy a product made from recycled materials if it did not appeal to you visually? I don’t think so!
You may be thinking that sustainability and recycled products do not exactly align with high-end and good quality. In this article, my aim is to show you that trash can be turned into treasure. Essentially, creating a new product in today’s world is a balancing act. It needs to be sustainable as well as visually appealing to a large audience to be truly successful.
RECYCLING POLYESTER
Recycling plastics like bottles, cups, bags, etc. has gained popularity as the go-to method to reuse our existing plastic and reduce its presence in our environment. Have you ever wondered how plastic bottles can be turned into yarn which is so soft!
Firstly, the collected plastic waste is segregated based on plastic type as there are many types of plastics being used in various industries. The PET (polyethylene terephthalate) based plastic products are the easiest to sort out as almost all packaged drink bottles are made from PET. There is also a plastic number stamped on all plastic products to help identify the kind of plastic used to make that product. The plastic number for PET is #1 making it very easy to double-check the segregated plastics.
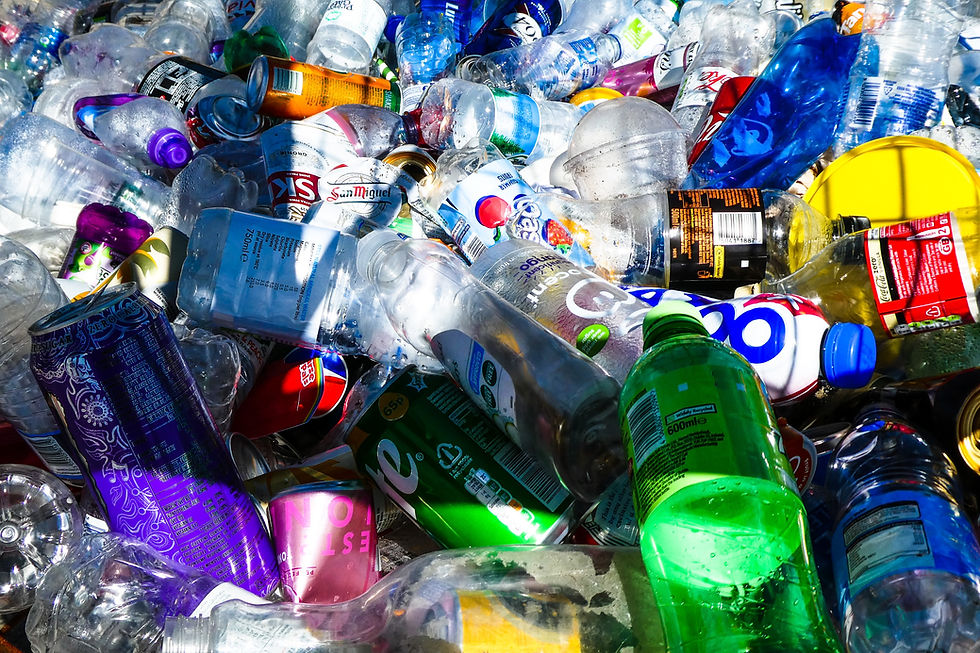
These bottles are then cleaned, sanitised and cut and chopped into flakes. The flakes are melted and converted into standardised pellets. This is done to ensure quality control in the extrusion which converts the pellets into long strands which are finally spun into yarns. A strict control on the melting temperatures and extruding processes allows for the yarn to be very soft.

The yarn may be mixed with other materials like cotton and wool to make various products. Many well-known brands have recently been in the limelight for making eye-catching products using recycled polyester like shoes, garments, rugs, upholstery fabrics, etc.
Currently, PET is the most recycled plastic because of its thermoplastic properties. The polymer chains break down at a relatively low temperature, and so there is no degradation of the polymer chain during the recycling process. Once melted, it is very easy to mould or extrude the melt into new shapes or filaments.
While developing Revival’s ‘Outside-In’ collection of outdoor-indoor rugs, we worked extensively with the plastic bottle recycling plant to get the appropriate texture of the recycled PET yarn. The yarn we developed was feather-soft to the touch without being shiny like plastic. A 5’x8’ rug contains about 460-500 recycled plastic bottles. The next step was creating a visually interesting weave where the colours almost ‘flowed’ from one another - like an expanded plaid-like pattern. I believe that it is this visual play of colours that first attracted customers to the product. The material is of course equally important. Most people could not believe that the yarns were once plastic bottles because the rug is so supple!

RECYCLING GARMENTS
It is no secret that thousands of tons of discarded garments end up in landfills on a regular basis. Fast fashion has cultivated the processes of quickly manufacturing trendy, inexpensive clothes in large volumes. People purchase these cheap clothes to wear a few times and then discard them when the trends change. We cannot make people change their lifestyle, but we can recycle these old garments into attractive new products.
India imports used garments from all over the world. According to the United Nations Comtrade database, India imported used garments worth $371 million in the year 2022. These used garments are segregated by colour and materials. The buttons, zippers, embroideries, etc. are removed and the garments are cut into small, long stripes called ‘chindi’ which are then washed for sanitation.

The next step is making a visually appealing new product with these ‘chindi’ fabrics. This was the challenge we faced while developing Revival’s ‘Denim Collection’ rugs made from recycled denim. We opted to use simple, geometric shapes with some art deco influences to highlight the mélange effect created by the denim. We also had to work with the manufacturer to ensure that the construction and finishing standards are met to ensure that the customers are receiving a sturdy, high-quality product. Since denim is a very sturdy textile itself, these rugs are machine washable, just like your jeans!
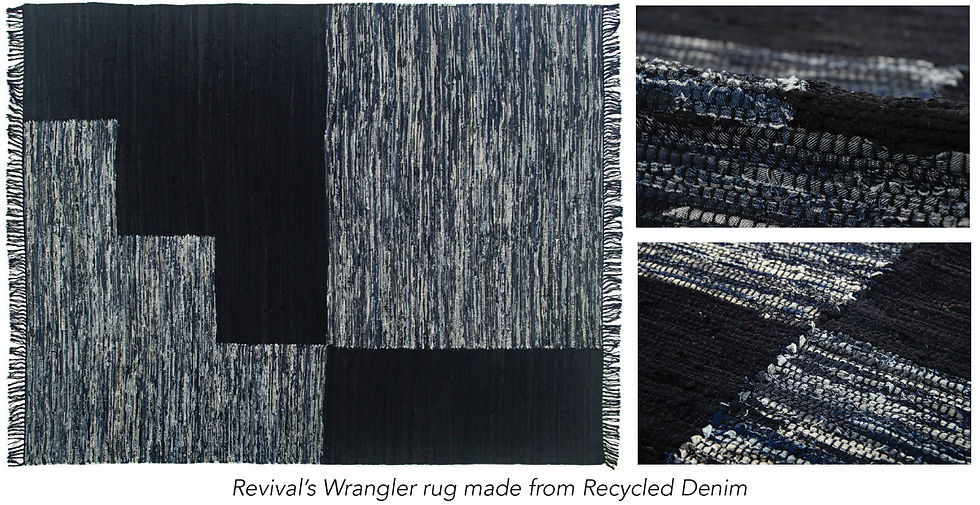
Many-a-times, the chindi is further broken down into fibres by intense shredding machinery. These fibres are spun into new yarn which are in-turn used to make entirely new products. As we developed Revival’s ‘Chindi Cushion Collection’ we not only used yarns made from recycled garments but also opted to work with small handloom weavers to weave the textile by hand. This was a double win for recycled materials and ethical labour practices!
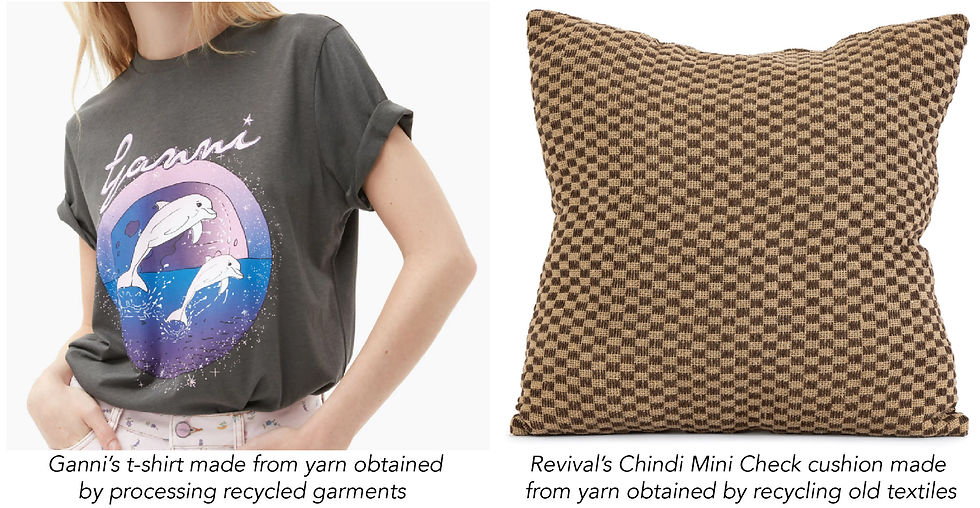
Globally, mainstream fashion and textile brands have recognised the need to incorporate sustainable practices making ‘recycled’ the new chic. By recycling our existing resources, we are preventing new resources from being wasted. Even if we can recycle only 1% of the billions of garments which end up in a landfill, that will still be a significantly large number of garments that are given a second life. The number of recycled products will only grow from here due to the world-wide rising awareness of the sustainability crisis.
PLANT – BASED LEATHERS
The development of new technologies has enabled the textile industry to create innovative materials. One such material is plant-based leathers. Let’s get one thing straight - plant-based leather is not real leather as there is no animal skin involved in the making process. Plant-based leathers are an altogether different material which look and feel like animal skin leather. The industry is currently abuzz with the advent of leather look-a-likes made from mushrooms, cactus and cork.
‘Desserto®’ is a highly sustainable plant-based material as an alternative to traditional leather. Cactus is harvested and the thorns are removed. The leaves are then chopped into small pieces and dried in the sun for 3-4 days. A chemical process is then performed on the dried pieces to extract cactus proteins and fibres in powder form. The powder is mixed with a resin to make a sticky paste-like substance. A thin layer of this paste is applied on a fabric base and dried slowly in a heating chamber to create the cracks which you see in real leather. The dried layer is then peeled off to give you Cactus leather! The same process is followed after harvesting cork bark to make cork-based leathers.
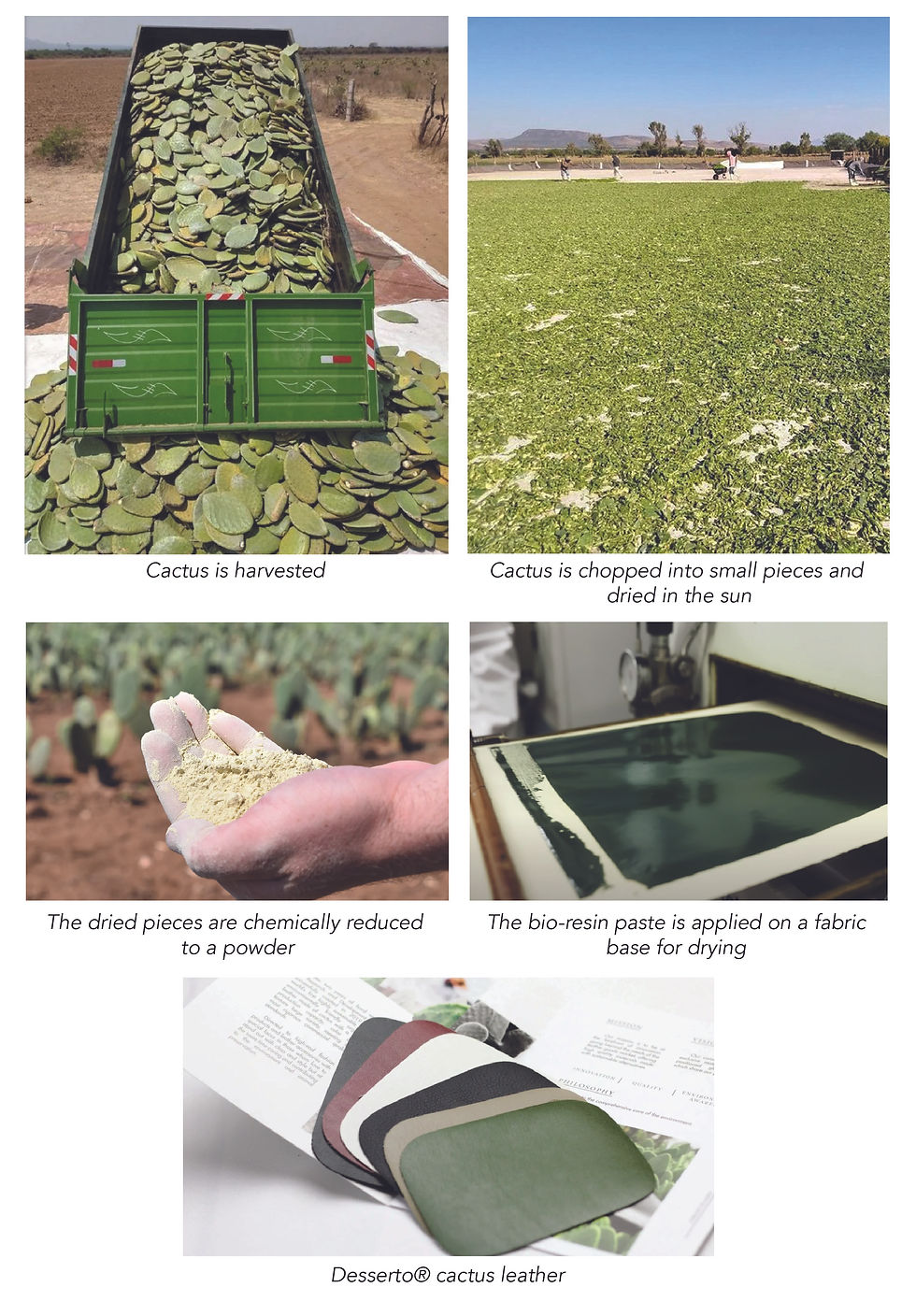
The process of making mushroom-based leathers is slightly different. Mushroom leather is actually made from mycelium. To understand what mycelium is, think of a tree with its stem and root networks in full bloom. The mushroom, which we know and love to eat, is actually the fruit of this tree. Whereas mycelium is the root system - the white thread like fibres which are seen surrounding any mushroom. The mycelium forms an interwoven network providing the nutrients required for the mushroom to grow.
A mixture of distilled water, mineral particles, starch, and hydrogen peroxide are poured into large trays and then injected with living mushroom cells. When placed in a dark environment, the cells start to grow by consuming the starch as food. In a matter of 2-3 weeks, a fine hair-like root network is formed in the entire tray. At this stage, a plasticiser is added in the tray in order to bind all the mycelium to a base. The mycelium sheet is then dried slowly and further treated to create the leather-like surface texture.

The ability to control the look, feel and colour of the final material is in itself a bio-engineering marvel. Plant-based leathers look and feel closer to real leather than PVC or PU leathers which is what makes them attractive to designers and brands. Today, these bio-leathers are being used not only to make bags but also garments, shoes, automobile seat covers and upholstery fabrics. Production of these materials can be scaled easily without being dependent on animal skins which are in relatively limited supply making them the best-available sustainable alternative to animal or plastic leathers.

Can you believe that such good-looking products are being made from recycled and sustainable materials? A recycled product is great for the Earth but as designers, we also have to ensure that the look and quality of the product is top-notch for a customer. Sustainable materials and good design are intrinsically linked at this point in time. If you purchase any product made from recycled materials or sustainable alternatives, you would want it to be visually appealing and feel authentic, right? Every designer should be able to put themselves in their customers shoes and ask, “does this product look high-end, or just a DIY project.”
Long-lasting change is possible only when mainstream retail products can be made from recycled and sustainable materials on a large scale. I truly believe that designers can play a crucial role in convincing upper management in a company to incorporate sustainable alternatives by showcasing the amazing products which can be made from such materials.
As published in ‘Design for All - Institute of India’, September 2023, Vol-18, No-9